Advanced NDT Techniques Used in Pressure Vessels
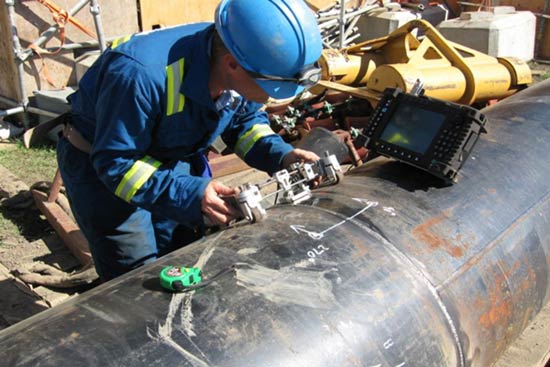
Non-destructive testing (NDT) is a vital interdisciplinary field that plays a critical role in pressure vessels. It ensures the equipment components, units, and any other complex systems carry out their various functions as effectively as they should. While doing so, they allow you to monitor the safety, the complexity of systems, and the cost-effectiveness. Advanced NDT techniques are in place to help pressure vessel manufacturers in India achieve the most reliable and safe pressure vessel equipment. Before we venture into learning about the NDT techniques used in pressure vessels, let’s understand what NDT actually is.
What is NDT?
Non-destructive testing (NDT) is a widespread pressure vessel testing and analysis technique in the process equipment industry. It aids in evaluating the properties of a material component and the structure of the characteristic differences. This is to ensure there are no welding problems or any discontinuities that may cause damage to the original part. NDT is also known as non-destructive evaluation, non-destructive examination, and non-destructive inspection.
What NDT Techniques Help With:
The NDT techniques have been put in place to help with the following;
- To measure
- Document corrosion
- Characterise
- Discover
- Cracks
- Wear and
- Any flaws that a pressure vessel and the piping systems may have that may otherwise lead to leaks or catastrophic failures.
Advanced NDT Techniques
Pressure vessels need handling with much care because of their hazardous and toxic gases. NDT techniques are vital to use as these minimise risks. Also, with better and proper observations and inspections, you can implement any of the advanced NDT techniques.
Phased Array Ultrasonic Testing (PAUT)
Phased Array Ultrasonic Testing or PAUT is an NDT technique and advanced application of ultrasonic testing. PAUT testing can offer a detail visualisation of the defect size, orientation, shape, and among other factors.
Long Range Ultrasonic Testing (LRUT)
With ultrasonic testing, you will need a pretty smooth surface finish because it uses only high-frequency sound waves to detect where the defect is. If there are cracked parts, the ultrasonic waves will reflect through them, giving out on the wall thickness. Furthermore, you may need water or gel as a coupling medium. After which, the ultrasonic probe will transfer the sound waves through the components detecting if there are any defects. The NDT technique has an automation system making it the best choice for any process equipment company because the manual application has some speed limitations.
Time of Flight Diffraction Testing (ToFD)
This NDT technique is applicable in situations where it’s impossible to obtain. On the other hand, true refraction but sufficient diffraction occurs, altering the time of flight of sound in a pitch-catch arrangement. It works best for detecting a defect’s tip that is perpendicular to the probe contact surface. It’s also the best for rear wall inspection to detect corrosion.
Advanced NDT techniques are ideal for pressure vessels. It offers a platform that covers various information at a given time. It’s the best way for pressure vessel manufacturers to gain knowledge and understand the NDT better, keeping society updated with any latest happenings in the global NDT domain.